In all my research and study of OSHA workplace standards over the years, I’ve yet to come across a specific requirement that employers must apply and document a job safety analysis (JSA) to comply with an OSHA standard. In fact, you don’t really see any references to JSAs within the text of OSHA’s volume of occupational safety and health standards. At the same time, OSHA points to job safety analysis as an essential tool for hazard recognition and control, worker safety training, and communicating safe work practices—all of which ARE core requirements at the heart of numerous OSHA standard requirements. In other words, JSA is integral to compliance with many aspects of a broad range of OSHA standards and is therefore a valuable tool that every safety professional should be using and improving on a regular basis.
If you’re a safety professional, you’re probably familiar with JSAs but might not be as familiar with how you can apply the information and findings they provide to address, document, and verify compliance with various OSHA requirements. If you’re not familiar with JSAs, here’s some quick background.
What is Job Safety Analysis?
There are numerous definitions of job safety analysis out there but at its core, JSA can be simply described as a “systematic method for identifying, assessing, and controlling job task hazards and risks.” It involves a six-step process that goes as follows:
- Job selection
- Job task breakdown
- Task hazard identification
- Task risk assessment
- Identification and implementation of controls
- JSA review
The ultimate output of a JSA is a detailed list of individual job tasks, recognized hazards of each job/task, the corresponding risk level of each hazard (usually in the form of a qualitative or semi-qualitative risk assessment), specific hazard controls required to minimize those risks, and an assessment of the control effectiveness for each recognized hazard. The completed JSA might look a little something like this:
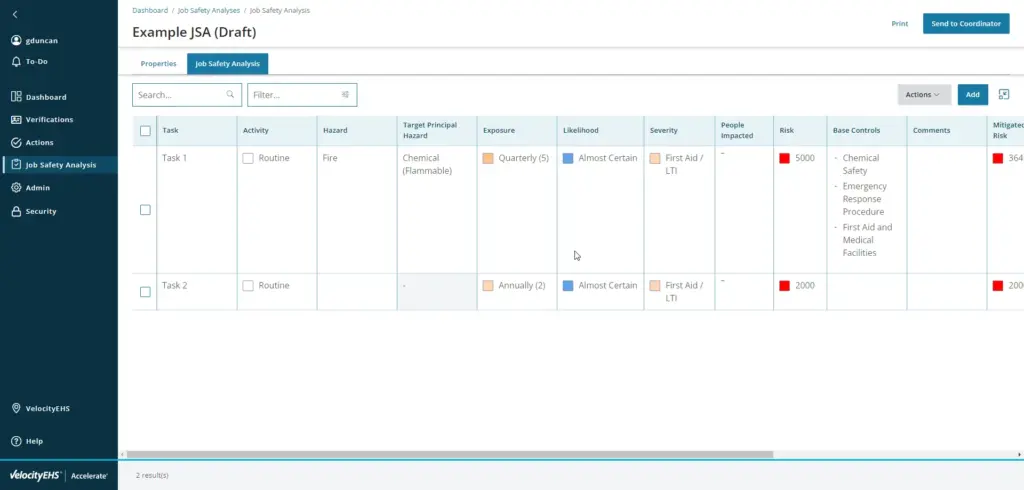
Sounds simple, right? While the process for documenting JSAs is a relatively straightforward exercise, there are many nuances that safety professionals and other members of your JSA team should be aware of to obtain the most accurate JSA information possible.
For more information on JSA techniques and best practices, view our on-demand webinar “Job Safety Analysis: Facts & Myths.”
How Can Job Safety Analysis (JSA) Help with OSHA Compliance?
There are nearly 1,000 distinct OSHA standards covering employers and jobs performed across the construction, maritime, agriculture and general industries, each with very specific and often prescriptive requirements. However, I would argue that all these standards have three common essential objectives: hazard recognition and control, worker safety training, and ensuring safe work practices. I would also argue that JSAs provide an ideal tool for performing and achieving all three of these objectives.
Hazard Recognition & Control
At the end of the day, safety is all about risk management – identifying hazards, evaluating the risks, and applying the most effective risk controls. This concept is the core of safety and underlies numerous OSHA standards:
Respiratory Protection Standard 1910.134(d)(1)(iii) – “The employer shall identify and evaluate the respiratory hazard(s) in the workplace; this evaluation shall include a reasonable estimate of employee exposures to respiratory hazard(s) and an identification of the contaminant’s chemical state and physical form. Where the employer cannot identify or reasonably estimate the employee exposure, the employer shall consider the atmosphere to be IDLH.”
Respirable Crystalline Silica 1926.1153(d)(2,3) – “The employer shall assess the exposure of each employee who is or may reasonably be expected to be exposed to respirable crystalline silica at or above the action level in accordance with [1926.1153(d)(2)(ii, iii)]. The employer shall use engineering and work practice controls to reduce and maintain employee exposure to respirable crystalline silica to or below the PEL, […]”
Personal Protective Equipment 1915.152(b) – The employer shall assess its work activity to determine whether there are hazards present, or likely to be present, which necessitate the employee’s use of PPE. If such hazards are present, or likely to be present, the employer shall […]”
Hazard Abatement Verification1903.19 – “The employer must inform affected employees and their representative(s) about abatement activities covered by this section by posting a copy of each document submitted to the Agency or a summary of the document near the place where the violation occurred.”
The list of standards rooted in the fundamental risk management process of identifying, assessing, controlling, and communicating workplace hazards goes on and on, and job safety analysis (JSA) offers an excellent tool for performing, documenting, and communicating every stage of this process.
Worker Safety Training
Safety training is also woven into nearly all OSHA standards, with more than 60 individual subparts of 29 CFR containing specific safety training requirements. At their core, however, all these requirements have a common purpose – to ensure workers have the training necessary to recognize hazards and work safely and ensure employers can demonstrate that they have provided that training.
Click here for more detailed information about Training Requirements in OSHA Standards
JSAs provide an ideal tool to identify training needs and corresponding training requirements, assign required training to the workers who perform the jobs being reviewed, and verify that required training has been completed.
For example, let’s say a worker needs to perform maintenance on a conveyor system in a food manufacturing facility. To repair the conveyor, the worker needs to shut down and isolate the conveyor system at the main control panel and potentially other isolation points, remove machine guards, and potentially risk exposure to unexpected release of hazardous mechanical or electrical energy.
This scenario would most definitely require a lockout/tagout (LOTO) procedure and trigger the requirements of the OSHA LOTO standard, including requirements to train workers on LOTO procedures and the function of the workplace LOTO program. In this example, compliance with the LOTO standard requires identifying what job task hazards are present, determining which tasks involve hazardous energy and are therefore covered under the OSHA LOTO standard, and satisfying any LOTO training requirements that are applicable to those job tasks. Because the JSA process is all about breaking a job down into tasks to better identify and control associated risks, it can help employers ensure that they don’t miss these kinds of job-critical training responsibilities.
This same basic process of job task hazard identification and delivery of required training is common to all OSHA training requirements. Fortunately, JSA provides a user-friendly format to identify applicable regulatory requirements, assign required training activities accordingly, and verify training compliance as you would with any other control prescribed under applicable OSHA standards.
Safe Work Practices
JSAs offer an excellent tool for safety professionals to identify training requirements and deliver required training to ensure compliance, but simultaneously provide an ideal format to communicate work instructions and safe work practices to employees. Remember, at a fundamental level a JSA is intended to break down a job task-by-task, identify the hazards present, specify necessary hazard controls, and spell out step-by-step instructions for how to perform each job task safely. This is an essential component of worker safety, which is why many OSHA standards contain requirements for employers to develop and communicate safe work practices to workers, including:
29 CFR 1910.333 Subpart S covering safe work practices in performing electrical installation and maintenance specifies that employers must develop and implement safety-related work practices “to prevent electric shock or other injuries resulting from either direct or indirect electrical contacts, when work is performed near or on equipment or circuits which are or may be energized. The specific safety-related work practices shall be consistent with the nature and extent of the associated electrical hazards.”
29 CFR 1926.502(k) covering fall protection systems criteria and practices establishes requirements for employers to develop and implement a fall protection plan that communicates fall protection measures applied in the workplace, identification of workers performing jobs where uncontrolled fall hazards are present, any changes to fall protection systems and hazards in those areas, and requires that “In the event an employee falls, or some other related, serious incident occurs, (e.g., a near miss) the employer shall investigate the circumstances of the fall or other incident to determine if the fall protection plan needs to be changed (e.g. new practices, procedures, or training) and shall implement those changes to prevent similar types of falls or incidents.”
29 CFR 1910.119 “Process safety management of highly hazardous chemicals” contains multiple requirements for development and communication of safe work practices including 1910.119(f)(4) stating that “The employer shall develop and implement safe work practices to provide for the control of hazards during operations such as lockout/tagout; confined space entry; opening process equipment or piping; and control over entrance into a facility by maintenance, contractor, laboratory, or other support personnel. These safe work practices shall apply to employees and contractor employees.” The standard continues at 1910.119(g)(1)(i) stating “Each employee presently involved in operating a process, and each employee before being involved in operating a newly assigned process, shall be trained in an overview of the process and in the operating procedures as specified in paragraph (f) of this section. The training shall include emphasis on the specific safety and health hazards, emergency operations including shutdown, and safe work practices applicable to the employee’s job tasks.”
1910.119(h)(2)(iv) “The employer shall develop and implement safe work practices consistent with paragraph (f)(4) of this section, to control the entrance, presence and exit of contract employers and contract employees in covered process areas.”1910.119(l)(5) “If a change covered by this paragraph results in a change in the operating procedures or practices required by paragraph (f) of this section, such procedures or practices shall be updated accordingly.”
1910.119(o)(1) “Employers shall certify that they have evaluated compliance with the provisions of this section at least every three years to verify that the procedures and practices developed under the standard are adequate and are being followed.”
There are numerous other OSHA standards requiring employers to develop and communicate safe work practices to workers, and JSAs offer an ideal means of doing so. I recently spoke at the 2024 Wisconsin Safety Conference and met with an attendee who approached me at the end of my session to share how they use their JSAs as a tool to communicate safe work practices to their workers. Basically, they print out their JSAs and post them at each corresponding workstation where each job is performed. In practice, the JSAs are used as an instruction manual for workers to operate that equipment and perform those jobs safely. I complimented the attendee that I thought this was an excellent use of their JSAs since in many cases they are often simply filed away, never really put to use, and rarely updated.
However, our conversation soon shifted to what systems their organization had in place to update their JSAs when new job task hazards are recognized, how those newly recognized hazards are communicated and controlled, how JSA safe work practices can be scaled across similar jobs and across multiple locations, and ultimately how those learnings are incorporated into safe work practices. That’s really the point where a paper-based JSA format fails. After all, if a JSA is inaccurate or incomplete and the true hazards of the job are not addressed within it, that job presents uncontrolled risks to workers.
JSA Brings it All Together
I’m a firm believer in the utility and value of JSAs as a tool for OSHA compliance. They’re a practical and valuable tool for inventorying applicable compliance requirements for each of the jobs performed in your workplace, documenting compliance with corresponding training requirements, and providing step-by-step safe work instructions in an easy to understand format to workers. In addition to all of that, they are a collaborative exercise in safety that provides an excellent opportunity to engage workers and other stakeholders in your safety program.
At VelocityEHS, one of the biggest barriers we hear about when talking to safety professionals is that most are still using paper-based systems to perform and document their JSAs. This imposes significant and unnecessary limitations when it comes to getting the greatest value from your JSAs, primarily because paper-based JSAs are, by their nature, static documents. A JSA should be a dynamic, living document that is easily communicated, responsive to the changing nature of training requirements and job hazards, and provides an easily accessible resource for workers to understand how to perform their jobs safely. With the right systems for managing your JSAs, you can realize all of the benefits that JSAs can provide to your safety and risk management programs and get the greatest value from them.
VelocityEHS can Help!
Risk management is the most fundamental purpose of any workplace safety program and our Operational Risk solution has the capabilities you need to do JSAs right. You get centralized, enterprise-wide visibility of your JSA processes to help you easily monitor hazards and control activities, standardize your risk assessment and scoring criteria, and take the guesswork out of JSAs with access to a consolidated control library that allows you quickly select the right controls for the jobs being reviewed. Most importantly, you’ll have the insights you need to assess performance and prioritize your workplace safety improvement efforts.
If you’re looking for a system to help you implement and coordinate a world-class safety program built around continuous improvement principles, we can help you there, too. Our Safety Solution gives you the support you’re looking for, with intuitive capabilities for inspections, audits, safety observations, incident investigations, safety meetings, compliance management, corrective actions, safety performance tracking and reporting, and much more.
Contact us today to learn more about how we can help you get the most from your JSAs and help you build a safer and more sustainable workplace.