Historically speaking, workers in the manufacturing industries are at higher risk for work-related injuries and illnesses than workers in other industries. In 2020, the manufacturing industry ranked fourth highest in non-fatal recordable injury and illness rates, with 3.1 cases per 100 full-time employees (FTE) compared to the average rate of 2.7 cases per 100 FTE across all private industries. The US Bureau of Labor Statistics (BLS) also shows that while manufacturing sectors employed 7.8% of the US labor force in 2021, they accounted for upwards of 9.5% of all non-fatal work-related injury and illness cases recorded that year. In addition, National Safety Council data shows that total number of non-fatal cases among manufacturing workers (135,900) rose by nearly 10% between 2019 and 2020, reaching their highest level since 2011. These figures and many others point toward an elevated risk of injury and illness for workers in the manufacturing industry, but they don’t tell us the entire story. The increasing utilization of temporary workers and contractors in manufacturing means that the risk of injury and illness for all manufacturing employees may be significantly higher than these figures suggest.
Temporary Workers & Contractors in Manufacturing
A 2020 study by Career Builder surveyed industries on their projected use of temporary employees. It found that information technology (IT) industries had the highest projected utilization, with 75% saying they planned to use temporary workers. Manufacturing industries ranked a not-too-distant second with 59% of employers planning on hiring temporary workers.
Temporary employment in manufacturing also continues to significantly outpace the average utilization rate compared to other industries. A 2018 BLS report analyzed data from the US Census Bureau’s Current Population Survey (CPS) and the US Department of Labor’s Occupational Employment Statistics Survey (OES) and revealed that since the Great Recession (2008-2017), utilization of temporary employees in the manufacturing industry ranged between 5.2% and 10.3%. Compare this to the overall average of around 2.0% for all industries during that same period.
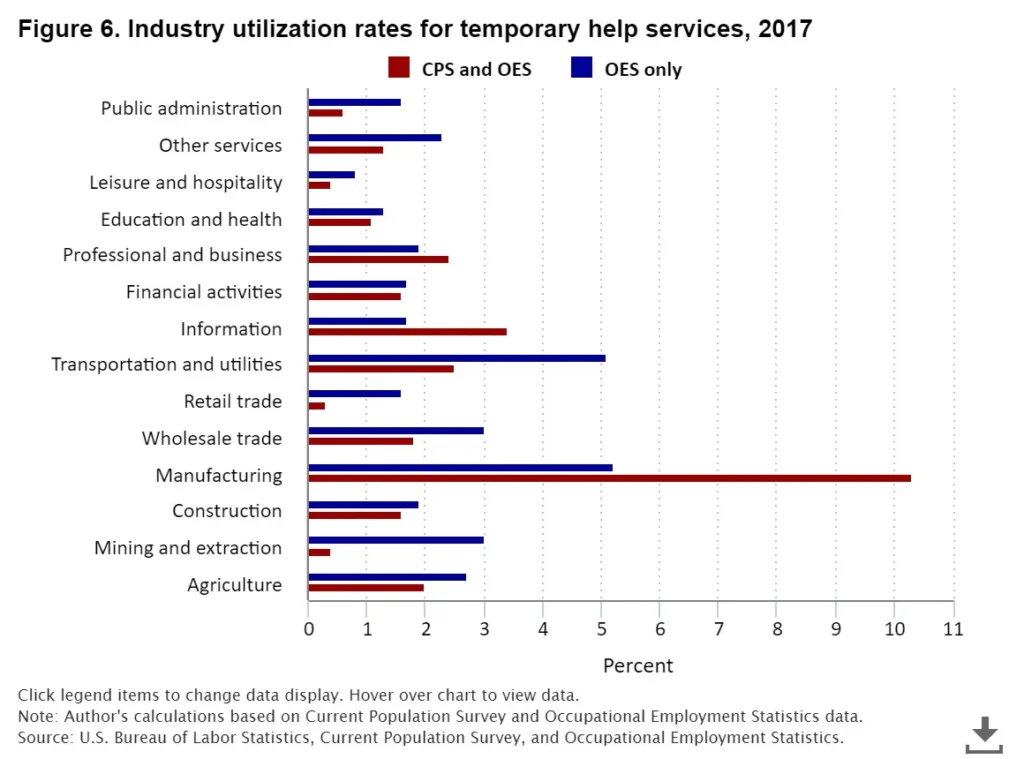
However, it’s important for manufacturers and other employers to remember that while temporary labor can provide significant financial and operational advantages compared to full-time permanent employees, those benefits can be quickly erased by overwhelming financial liabilities and damage to your business if temporary worker safety is poorly managed.
Numerous studies show that temporary workers are at elevated risk for workplace injury and illness. An analysis performed by researchers at ProPublica.org looked at worker’s compensation claims in several states between 2007 and 2012 and found that the incidence of workplace injuries for temporary workers was between 36-72% higher than that for full-time regular employees.
Another study conducted by the National Council for Occupational Safety & Health (NCOSH) showed that temporary workers, who represent just 2% of the U.S. workforce, accounted for 17% of work-related fatalities in 2015. Other research performed by the Washington State Department of Labor & Industries found that temporary workers in construction and manufacturing had twice the rate workers’ compensation claims compared to full-time regular employees doing the exact same types of work.
When you consider the elevated risk of injury and illness among temporary employees in combination with the upward trend in temporary labor in the manufacturing industry, it’s not hard to imagine how this could contribute to potentially higher rates of injuries and illnesses.
The first step to prevent these injuries and illnesses is understanding their root causes. So, what’s behind these higher rates of injury and illness among temporary workers and contractors? Manufacturers, like most other employers, generally possess a lesser degree of control over the performance of temporary employees and contractors than over their own full-time permanent employees when it comes to workplace safety. Poor communication of training and hazard information, along with confusion between host and temporary employers regarding each parties’ obligations for temporary worker safety are major contributing factors.
The findings of these studies and others like them suggest an inconvenient truth for employers—bringing temporary employees or contractors into your workplace is likely to introduce additional EHS risks to your business and your employees. Yet, despite these added risks, the utilization of temporary workers and contractors in the manufacturing industry continues to rise.
Therefore, employers should strive to provide added layers of protection when temporary workers and contractors are on-site. That way, employers can ensure that all work is being performed in accordance with their own high safety performance standards, and they are doing all they can to protect workers. That’s where the value of a formal Control of Work (CoW) system really comes into play.
What is Control of Work?
A Control of Work (CoW) system is an essential element of a comprehensive EHS management program that functions to ensure that all temporary workers and contractors (as well as the staffing agencies and contractor providers who employ them) meet the qualifications and safety standards of your organization, support safe facility operations, and align with your safety performance goals. At the same time, the system gives employers’ a formal system to document and track temporary workers on-site, and enhances employers’ visibility and control over the wide range of temporary work activities being performed within your facilities at any given time.
CoW systems also support effective application of the contractor safety management lifecycle (Figure 1), which provides a formal framework for planning, evaluation and selection, implementation, onboarding/induction, and safety performance review of contractors and temporary workers.
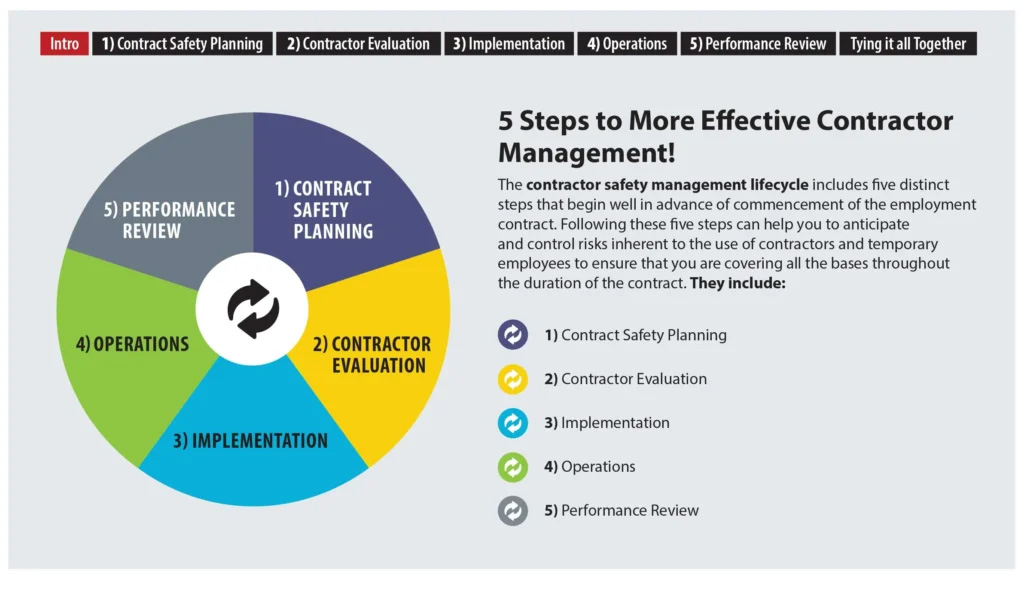
The contractor safety management lifecycle blends CoW processes with continuous improvement principles so that data, best practices and lessons learned throughout can be integrated into the system, ideally refining your CoW system with each iteration. To learn all about Control of Work systems and the contractor safety management lifecycle, including a detailed breakdown of each step, watch our on-demand webinar “Ensuring 100% Certainty with Contractor Safety & Compliance” and download our interactive infographic “Applying a Systematic Approach to Contractor Management.”
CoW and Permit-to-Work (PTW)
An important and often requisite component of CoW and contractor/temporary worker safety is implementation and maintenance of a Permit-to-Work (PTW) system. It can be helpful to think of PTW as a sub-system that provides an added layer of protection within your CoW system.
PTW systems provide manufacturers with a formal, standardized process to identify, document and evaluate job hazards, and verify that all prescribed hazard controls, training, precautions, and personnel are in place prior to commencement of contract or temporary work. At the heart of a PTW system is the permit-to-work or “permit.” It is a physical or electronic document that specifies all associated job hazards and provides verification in black-and-white that a worker possesses the necessary qualifications and hazard controls to safely perform a specific task. Information typically included/required on the permit will include (but is not limited to):
- Names of specified personnel who are authorized to perform work at a specific site at a certain time
- A detailed list of the hazards of the job, and the corresponding hazard controls, training and other precautions necessary to perform the job safely
- Written verification and approval from a permitting authority that the permit holder is qualified to perform the work, and that all necessary controls and precautions are in place prior to performance of work
- The timeframe of the permit. Permits are typically issued for a specified duration and must be either “closed” when work is complete or otherwise concluded, or specify procedures for renewal where necessary.
PTW Requirements & Best Practices
In many jurisdictions, permits must be issued and maintained when employees (whether contract/temporary or permanent) perform specific types of high-hazard jobs such as hot work (welding, cutting, brazing, etc.), confined space entry, work at height, live electrical work and isolation of hazardous energy (i.e. lockout/tagout). Depending on applicable occupational health and safety standards, the following types of hazardous work likely require use of PTW:
- Electrical work (high/low voltage)
- Mechanical service & maintenance
- Utilities
- Hot work
- Confined space entry
- Excavation/trenching
- Hazardous material handling/disposal/remediation
- Work at heights
- Heavy equipment operation
- Scaffolding
Even when PTW is not specifically required by applicable occupational health and safety standards, it is best practice to use permits for any manufacturing job where workers may be exposed to hazard which they may be unfamiliar with, where special precautions or additional hazard controls are needed, or where there is a potential for miscommunication of hazards between employers or employees that could create a risk for injury or illness. Types of jobs where PTW should be used include:
- Non-production work (e.g. maintenance, repair, inspection, testing, alteration, construction, dismantling, modification, cleaning etc.)
- Non-routine operations
- Jobs where two or more individuals or groups need to co-ordinate activities to complete the job safely
- Jobs where there is a transfer of work and responsibilities from one group to another
For a more detailed look at PTW systems and best practices for implementing and maintaining a PTW system in your workplace, watch our on-demand webinar “Permit-to-Work (PTW) Systems: Real-World Best Practices to Optimize Your Process.”
The Value of CoW & PTW
As mentioned earlier, CoW and PTW systems provide manufacturers with a highly visible and traceable means of verifying that temporary workers possess the necessary skills, training, and hazard controls to perform jobs safely. CoW and PTW systems also provide assurance that temporary employers like contractor providers and staffing agencies meet your requirements with respect to regulatory compliance, safety performance, liability coverage, or any other qualifications and criteria you set forth. From an administrative standpoint, they also provide enhanced visibility of work activities across multiple facilities and inform more detailed safe work plans (SWPs) that effectively address the hazards that may be introduced into your workplace due to the presence and activities of contract and temporary workers.
The ability to monitor what jobs are being performed, when and where they are being performed, and who is performing those jobs is also a valuable advantage for departments outside of EHS. HR, facility security, maintenance, operations, payroll, and many other teams benefit from the ability to schedule, coordinate, and monitor the presence of temporary workers and contractors on-site.
Last but certainly not least, formal CoW and PTW systems provide an effective communication framework that promotes collaboration and coordination between host and temporary employers. This makes it easier to ensure all parties to the employment contract are aware of their obligations for temporary worker safety, and verify that all necessary training, hazard controls, personal protective equipment (PPE) and other job-specific precautions are in place prior to work. This understanding and communication is a crucial, yet often overlooked component of contractor and temporary worker safety, the lack of which has been shown to be a significant factor in temporary worker injuries and illnesses.
Control of Work Challenges
As you might imagine, effective CoW and PTW systems have a lot of moving parts and involve participation and communication among multiple individuals and employers. The unfortunate fact is that an overwhelming majority of businesses rely on basic software like email, spreadsheets, word documents, and paper-based permits to manage their CoW and PTW systems. This creates a high potential for error and unnecessary bottlenecks in the contractor safety management and permitting processes which, at the very least, can delay contractors and temporary workers from entering your facilities and getting the job done. At worst, it can lead to gaps in hazard awareness and communication failures that can put temporary workers and contractors, as well as your own workforce at risk.
A 2017 study in the journal Chemical Engineering Transactions looked at more than 600 process safety-related accidents in the chemical processing and manufacturing industries between 1990 and 2015, and found that permit-to-work (PTW) system failures were identified as the root cause in 6.98% of the 600 cases studied.
By itself, this might not seem like a significant contributor to the overall number of process safety-related accidents, but the study also noted that the percentage of accidents caused by PTW system failures had not improved year-over-year during the 25-year period of the study. The study also found that in every case where PTW system failures contributed to process safety-related accidents, poor communication of essential hazard information and improper or missing safe work procedures contained within the permit were found to have contributed to the failure.
A separate 2016 study from the National Institutes of Health (NIH) concluded that adherence to a formal permit review process and automation of PTW issuance procedures can be very effective in overcoming the limitations of paper-based PTW systems, and can prevent or reduce the probability of human errors in the permitting process.
Additional Control of Work Resources
Check out these additional resources to learn more about how to implement and optimize your CoW and PTW systems:
- What is Control of Work?
- Implementing a Digital Contractor Management System: A Panel Discussion with Customers – Webinar Discussion Summary
- The Burdens of Permit to Work and Contractor Management
- ePermits vs Paper Permits – Making the Move to an Electronic Permit to Work System
- The Issue with Incomplete Permits
- The Perils of a Paper Permit System
VelocityEHS can Help!
Control of Work is a critical component of managing operational risk at every level of a global enterprise. With permit-to-work, contractor management, visitor management, and additional CoW tools, the VelocityEHS® Control of Work solution can ensure temporary workers and contractors have been properly vetted, trained, and approved. VelocityEHS® Control of Work helps manufacturers and employers across all industries seamlessly manage complete contractor journeys and electronic permit-to-work processes across locations through a single centralized system.
VelocityEHS® Control of Work includes an all-in-one PTW system that can be easily configured to match your organization’s specific PTW processes to improve visibility of health and safety policies throughout the workplace and connect workers to what’s actually happening in your organization. By providing greater transparency, strengthening compliance with EHS policies, and structuring your PTW system in a way that prompts workers to complete permits thoroughly and accurately, electronic PTW systems can save manufacturers significant time and headaches with day-to-day tasks while minimizing EHS risks.
Visit our Control of Work Solutions page to learn more.