Easy-to-Use Management of Change Software
Complex process changes require precise coordination and oversight. For those in highly process oriented industries, Management of Change (MoC) is not just a nice to have, it’s a regulatory requirement. Great news: MOC is available on the Accelerate Platform.
Simplify change management with controlled workflows
Track and manage change requests with full visibility
Easily generate reports on the current status of all changes
The Management of Change Solution, part of the VelocityEHS Accelerate® Platform, streamlines complex processes for evaluating the impacts of organizational process changes. It’s designed to give you the flexibility needed to manage organizational change anywhere, anytime.
Core Capabilities
Workflow Management
Take control of critical workflows with greater visibility.
Pre Start-Up Checklist
Deploy custom checklists to ensure a safe and successful start.
Post Start-Up Checklist
Minimize risks post change with custom checklists to ensure follow through.
Status Notifications
Automate alerts to stakeholders to drive engagement and oversight.
Audit Trail
Automatically preserve a record of activities, participants, dates, and completions.
Workflow Management
Take control of critical workflows with greater visibility.
Pre Start-Up Checklist
Deploy custom checklists to ensure a safe and successful start.
Post Start-Up Checklist
Minimize risks post change with custom checklists to ensure follow through.
Status Notifications
Automate alerts to stakeholders to drive engagement and oversight.
Audit Trail
Automatically preserve a record of activities, participants, dates, and completions.
Webinar
Management of Change (MOC): Strategies for Compliance
This on-demand webinar reviews the applicable MOC regulatory requirements, while also focusing on the ultimate goal of protecting the safety and health of employees, increasing employee engagement, and improving safety and health performance.
Benefits of VelocityEHS
Management of Change Software
Reduce Operational Change Complexity
- Maintain a record of changes/approvals
- Control workflows with integrated approvals
- Access customizable implementation checklists
Gain Enterprise-Wide
Visibility
- Provide change management program transparency
- Track change requests & implementation action items
- Send escalating deadline email notifications
Streamline Tasks & Simplify Compliance
- Produce audits & reports on the status of changes
- Ensure compliance with OSHA’s PSM regulations
- Create a clean audit trail with efficient tracking at each stage
The EHS Software Revolution Has Begun
Introducing the VelocityEHS
Accelerate® Platform
The industry’s first truly integrated EHS platform on the market, streamlining Velocity’s Safety, Ergonomics, Chemical Management, and Operational Risk capabilities into one seamless solution.
Activations are underway. Secure your spot today!
Prevent Harm
Send workers home safe with solutions that cover a range of risks.
Drive Engagement
Reduce training time and simplify complex tasks with in-app guides.
Save Time
Free managers from tedious administration with centralized controls.
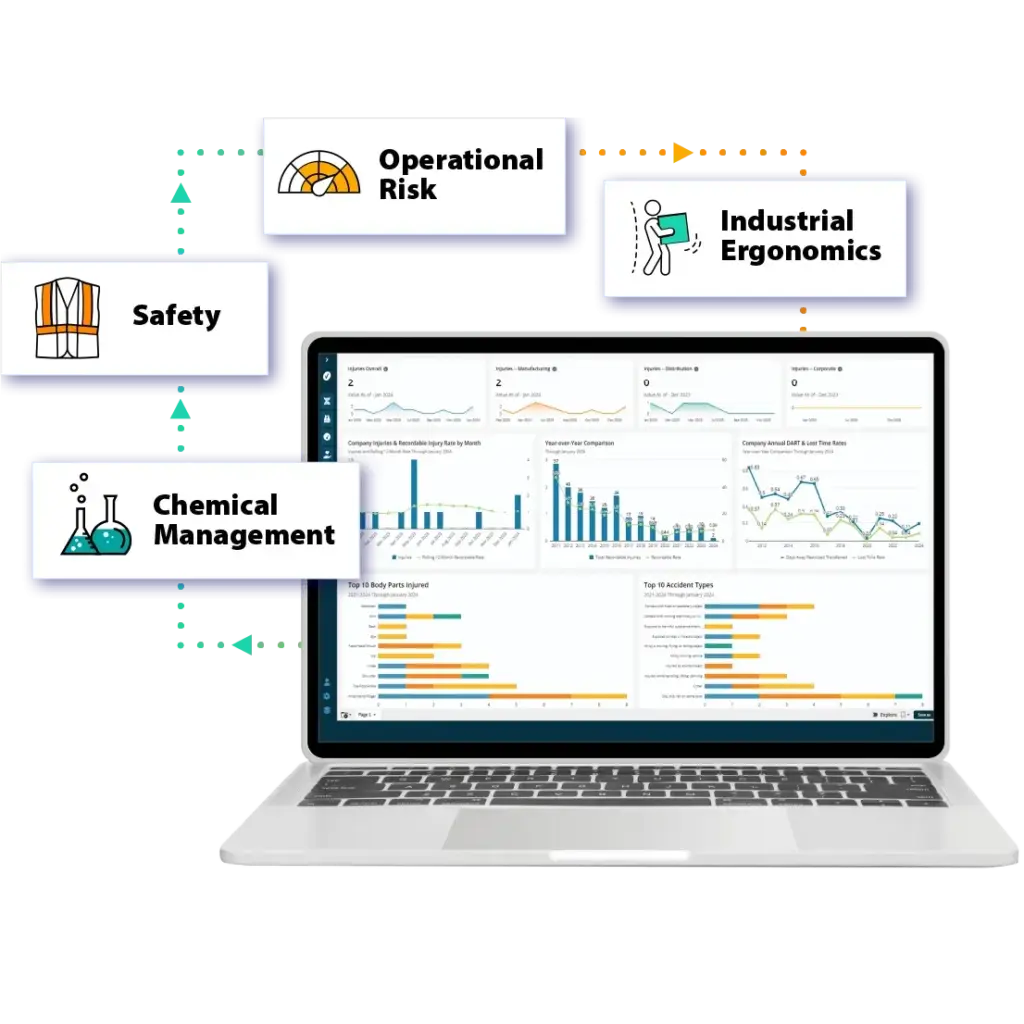
Be Predictive
Anticipate & address risk with real-time data you can trust.
Increase Visibility
Unite every level of your organization via shared dashboards & reports.
Embrace Innovation
Harness machine learning + AI & automation to deliver expert-level results, faster.
What our customers say…
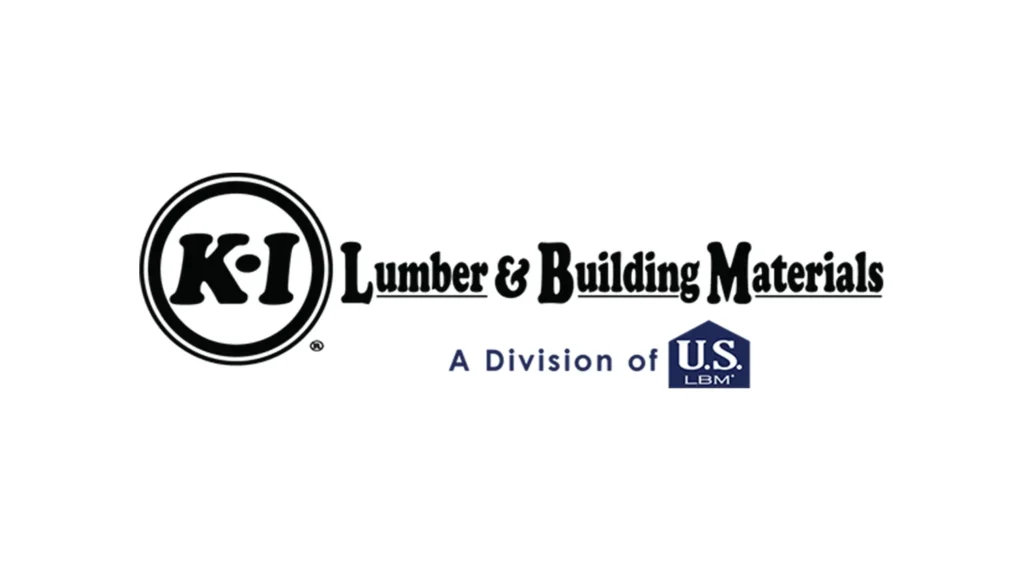
“Excellent service. The software is user-friendly. The program satisfies my needs.”
Continue reading about VelocityEHS
Management of Change Software
Helpful Resources
What’s New in Operational Risk?
Check out the latest operational risk industry news, our latest blogs, and helpful training resources to ensure you stay ahead of the curve.
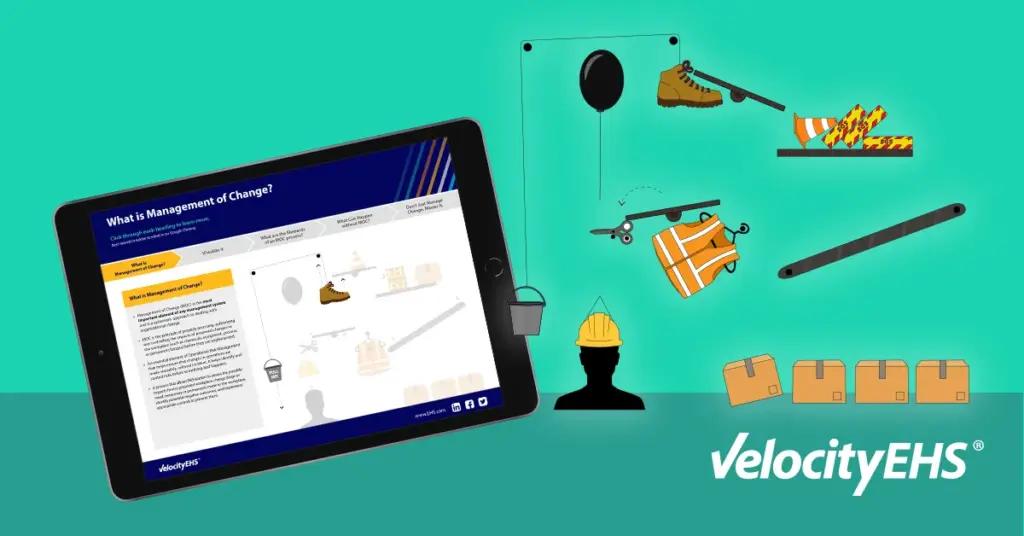
What is Management of Change? Infographic
Infographic
Operational Risk
Download this infographic to better understand Management of Change and how to master it at your organization.
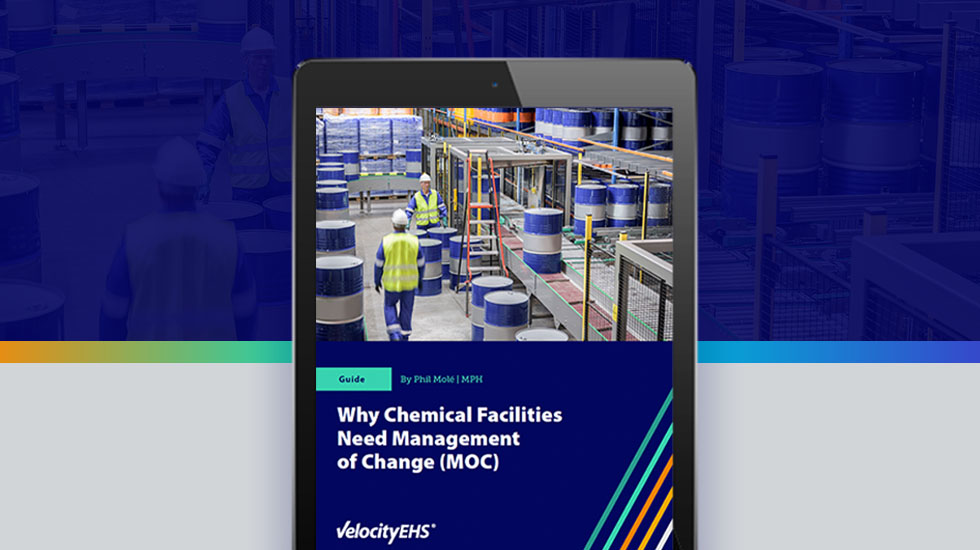
Why Chemical Facilities Need Management of Change (MOC)
Guide
Operational Risk
Download this guide now to learn the benefits of effective MOC processes in the chemical industry.
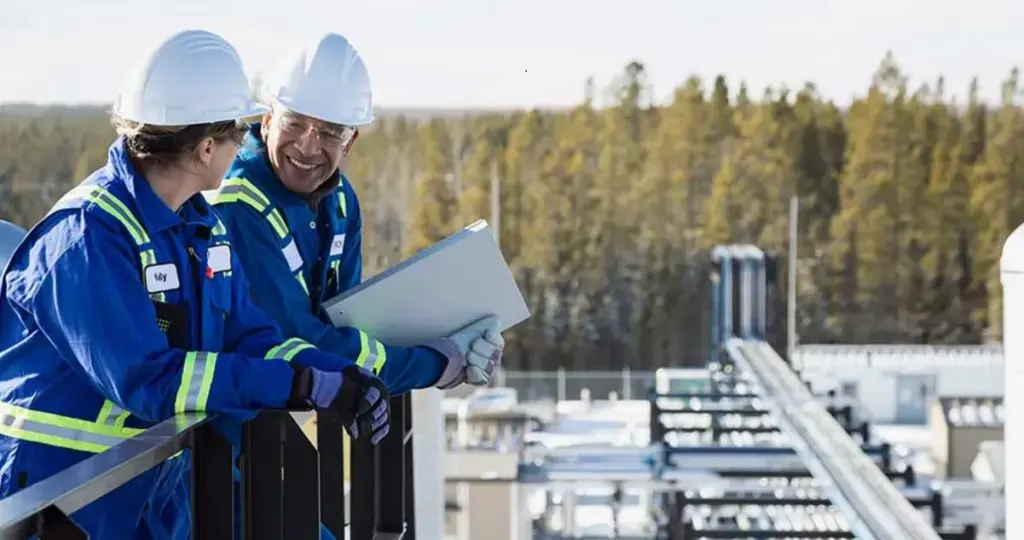
Integrating Risk Assessments for Effective Management of Change
On Demand Webinar
Operational Risk
This webinar explores the dynamic relationship between Management of Change (MOC) and risk assessments, focusing on the types of assessments required for different ch…
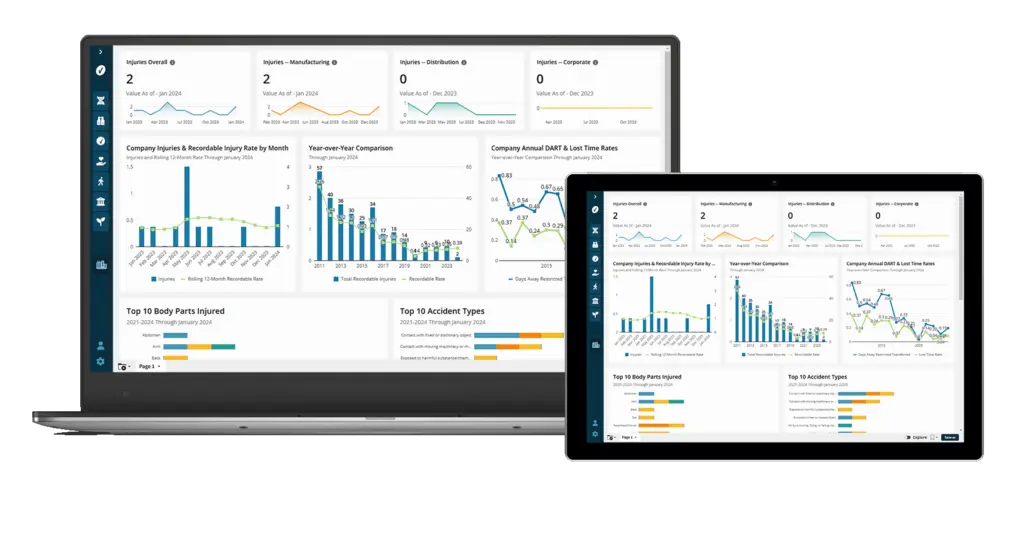
Schedule a Demo Today
You’re not just buying software or services—you’re investing in a partnership that empowers your team to proactively solve problems and move boldly into the future.