by Phil Molé, MPH
It’s been a busy year for OSHA, with the agency taking quite a few notable enforcement and regulatory actions already in 2022—and the year isn’t over yet! Judging by the White House’s recent Spring Unified Agenda covering all federal agencies, OSHA has more big plans in the works.
It can feel like a full-time job just keeping up with the pace of regulatory changes affecting your business, not to mention all the other responsibilities on your plate, but we’re here to help. In what follows, we’ll cover some of the most important recent OSHA regulatory and enforcement actions, as well as the items on OSHA’s Regulatory Agenda you most need to know.
As always, we’ll also boil things down to a few key takeaways at the end and explain how modern EHS & ESG software can help.
#1: OSHA’s HazCom Proposed Rule
OSHA’s Hazard Communication Standard (HazCom) is a good place to start since it’s arguably the most impactful and far-reaching of the regulatory changes we’ll be discussing.
On February 16, 2021, OSHA published a long-awaited notice of proposed rulemaking (NPRM) to update the HazCom Standard by aligning it with Revision 7 of the UN’s Globally Harmonized System of Classification and Labelling of Chemicals (GHS). The NPRM proposes major updates, including revised classifications for flammable gases, aerosols and desensitized explosives, revised requirements for “small” and “very small” shipped containers, revised shipping requirements for “bulk shipments,” and requirements for classification of hazards under “normal conditions of use,” including those resulting from chemical reactions and physical changes. The NPRM would require manufacturers of substances to comply with these new requirements within one year of the effective date of the eventual final rule, while manufacturers of mixtures would have two years from that final rule effective date.
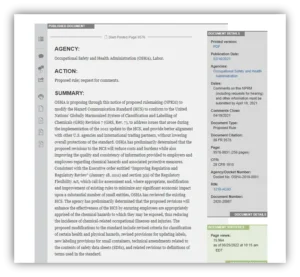
OSHA’s HazCom NPRM
For a deeper dive into the provisions of the HazCom NPRM, check out our eBook, A Deeper Look at OSHA’s Proposed GHS Revision 7 Update to the HazCom Standard.
The proposed changes would have impacts throughout the chemical supply chain, especially on manufacturers of affected chemical products. As a result, OSHA received a great deal of stakeholder feedback before the public comment period ended on May 19, 2021. OSHA also held a public hearing on September 21-23, 2021, to allow additional commentary by stakeholders who’d submitted a Notice of Intent to Appear (NOITA) by the established deadline.
According to the 2022 Regulatory Agenda, OSHA is targeting a publication date of December 2022 for publishing the final rule to update HazCom. It remains to be seen if they’ll stick to that timeline, but once the final rule is published, it will start the compliance clock. We’ll need to wait for that final rule to see if OSHA changes the phased-in compliance timeline from the NPRM, because many industry representatives who participated in the 2021 public hearing stated that the timeline for manufacturers of both substances and mixtures wasn’t long enough. One thing we can be sure of is that big changes are coming, and companies throughout the chemical supply chain will need to prepare.
#2: OSHA’s Recordkeeping Proposed Rule
OSHA published an NPRM on March 30, 2022 that would significantly revise electronic injury and illness reporting requirements for many US workplaces. Let’s look at the major proposed changes in the NPRM and see how they might affect you.
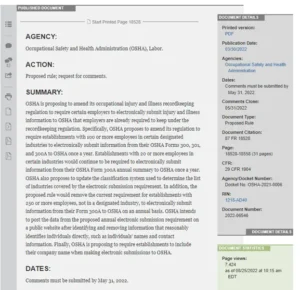
OSHA’s Recordkeeping NPRM
Expanded Reporting Requirements: The NPRM proposes to require establishments with 100 or more employees in certain designated industries to electronically submit information from their OSHA Forms 300, 301, and 300A to OSHA once each year. This would be a major expansion of reporting requirements for many establishments.
The industries affected by this proposed requirement would be listed in appendix B to subpart E of the Recordkeeping Standard. All establishments with 100 or more employees in industries listed in the proposed Appendix B to subpart E are already required to electronically submit Form 300A data to OSHA once a year under current requirements but would now need to additionally submit data from their Forms 300 and 301. For more information about affected NAICS codes, check out our earlier blog on this topic.
Publication of Data: The NPRM states that “OSHA intends to post the data from the proposed annual electronic submission requirement on a public website after identifying and removing information that reasonably identifies individuals directly, such as individuals’ names and contact information.” Many comments submitted in the docket for the NPRM express concerns about this provision. Remember that 300A data received from establishments covered by current electronic reporting requirements only contains summary level info about numbers of certain types of injury and illness cases, but the 300 and 301 forms contain much more specific information (including personally identifiable information) about individual cases. Stakeholders are understandably concerned about the feasibility of removing all potentially identifying information from these records and about how employees can be assured that their confidential information will remain protected.
There would also be reduced reporting requirements for some establishments, because the NPRM would remove the current requirement for establishments with 250 or more employees, not in a designated industry, to electronically submit information from their Form 300A to OSHA each year.
The public comment period for the recordkeeping NPRM closed on May 31, 2022.
#3: OSHA’s Planned Lockout-Tagout (LOTO) Update
OSHA’s “Control of Hazardous Energy” standard, most commonly known as “Lockout Tagout” (LOTO), has a long history going back to initial solicitation of stakeholder input in 1980 and publication of the first final rule in 1989. The requirements, found in 29 CFR 1910.147, have been largely unchanged ever since then, even though technologies like computer-based safety controls are now recognized and incorporated into similar hazardous energy control standards around the world.
OSHA has long discussed the potential need for an update, and in May 2019 issued a Request for Information (RFI) to solicit information from stakeholders on the strengths and limitations of modern technology for controlling hazardous energy. The 2019 RFI notes, for example, that the LOTO standard currently specifies that control circuit devices cannot be used as energy-isolating devices, but that “the agency recognizes recent technological advances may have improved the safety of control circuit-type devices.”
The Spring Regulatory Agenda provides evidence that OSHA has worked through and weighed feedback submitted through the RFI process and is preparing to initiate rulemaking to update the LOTO standard. The Reginfo page for the initiative indicates a projected date of March 2023 for an NPRM. That rulemaking will have far-reaching impacts because of the broad applicability of the LOTO standard. Employers will want to pay careful attention to OSHA’s updates and their implications for workplace safety and regulatory compliance.
#4: OSHA’s Planned Silica Update
A little background is necessary to understand the significance of OSHA’s planned regulatory updates to its existing respirable crystalline silica (RCS) standard.
In 2016, OSHA issued two new standards for respiratory crystalline silica (RCS) – one for general industry and maritime (29 CFR § 1910.1053) and one for construction (29 CFR § 1926.115).
The 2016 standards established a new exposure action level (AL) of 25 µg/m3 and reduced the silica PEL from 100 to 50 µg/m3— both calculated as 8-hour time-weighted averages (TWAs). The standards also include requirements for installing exposure controls, implementing medical surveillance programs to monitor workers’ health and exposure to RCS, and maintaining a written exposure control plan.
Some stakeholders weren’t satisfied with the level of protection provided by the 2016 final rules, specifically taking issue that the rules contained medical surveillance provisions but not medical removal provisions. Many OSHA standards for other chemicals have medical removal provisions such as lead, cadmium and formaldehyde. Each require the employer to monitor certain exposure indicators such as airborne concentrations of chemicals or bloodborne concentrations (as in the case of lead exposure) and remove the employee from the source of exposure once specified maximum levels are reached. Following publication of the 2016 final rules, the US Court of Appeals for the District of Columbia Circuit concluded that OSHA failed to adequately explain its decision to omit medical removal protections from the rule and remanded the rule for further consideration of the issue, which brings us to the current state of rulemaking.
The Spring Regulatory Agenda contains an initiative called “Occupational Exposure to Crystalline Silica: Revisions to Medical Surveillance Provisions for Medical Removal Protection,” and the title really tells the story. OSHA is planning to revisit the silica rules to include medical removal provisions, and the Reginfo page (see below) indicates an estimated timeframe of May 2023 for publication of an NPRM.
OSHA’s planned rulemaking would significantly impact affected industries, which include many cement and asphalt manufacturing and construction facilities. We should also note significant link to OSHA’s Recordkeeping Standard here because medical removal cases count as recordable injuries—either as “days away from work” or “restricted duty” depending on whether the employer complies by completely keeping the employee off work or by just changing their work duties to reduce silica exposure. Employers subject to the silica rules will need to be sure they have thorough workplace inspection and industrial hygiene (IH) medical surveillance programs in place, but an efficient incident management system to enable prompt recording of medical removal cases.
#5: OSHA’s Regulatory Activities on Heat Exposure
According to the U.S. Department of Labor’s Bureau of Labor Statistics (BLS), the effects of hazardous heat exposure resulted in an average of 35 fatalities per year and 2,700 cases with multiple days away from work between 2015 and 2019. The actual numbers may be higher, because the BLS indicates that heat-related fatalities may be underreported and improperly diagnosed due to failures to document when exposures to heat caused or contributed to “official” causes of death, such as heart attacks.
As a result, OSHA has been stepping up its efforts to protect employees from hazardous heat exposure. Let’s discuss some of its most recent initiatives.
OSHA’s National Emphasis Program (NEP) on Heat Exposure
OSHA rolled out a new NEP on “Outdoor and Indoor Heat-Related Hazards” on April 8, 2022. The NEP lays out OSHA’s inspection and enforcement priorities to support reduction of occupational illnesses and fatalities from heat exposure.
OSHA’s NEP contains an Appendix A of “Target Industries for the NEP” that lists the North American Industrial Classification System (NAICS) sectors that they’ll be focusing on for targeted inspection activities. According to the NEP, inclusion of an NAICS code in Appendix A is based on factors including high numbers or high incidence rates of heat related illnesses from the Bureau of Labor Statistics (BLS) data, especially severe cases, and numbers of heat-related general duty clause 5(a)(1) violations.
The NEP states that programmed inspections will occur on days that the National Weather Service (NWS) has announced heat warnings or advisories for the local area. According to the NEP, OSHA’s compliance safety and health officers (CSHOs) conducting a site inspection will open or refer a heat-related case incident for any hazardous heat conditions observed or recorded by the employer in the OSHA 300 logs or 301 reports they’re required to maintain under the Recordkeeping Standard. CSHOs will also open a case if an employee reports heat-related hazard(s) such as lack of access to rest or shade, lack of acclimatization, and lack of proper training about heat hazards during an inspection.
The NEP is currently in effect and applies “OSHA-wide” (everywhere under federal OSHA’s jurisdiction). States with federally approved state OSHA plans are not required to adopt the NEP, but if they do so, they must adopt provisions at least as stringent as the federal NEP.
OSHA’s Advanced Notice of Proposed Rulemaking (ANPR) on Heat Exposures
OSHA published an ANPRM in the Federal Register on October 27, 2021 to initiate the process of work on a heat exposure standard. According to an agency info page for the ANPRM, its purpose is to “more clearly set forth employer obligations and the measures necessary to more effectively protect employees from hazardous heat.” OSHA also produced a fact sheet on the ANPRM as shown below.
An ANPRM indicates that OSHA is planning a rulemaking and is looking for technical expertise and stakeholder feedback to guide that process. In this instance, OSHA stated they were specifically seeking feedback on the scope of a potential standard, heat stress thresholds for workers across various industries, heat exposure monitoring, and the types of controls employers should use. OSHA also sought stakeholder feedback on heat acclimatization planning. The term acclimatization refers to an employee’s build-up of resistance to heat exposure over time. Existing guidelines by organizations such as the Centers for Disease Control and Prevention (CDC) have implications for how employers might use heat acclimatization as part of their plans to protect workers from harmful heat exposures. For example, because acclimatization builds over time, employers should not assign a new employee who has not built up their heat resistance to work a long shift in a hot environment.
The public comment period for the ANPRM closed on January 26, 2022. OSHA also held a public hearing on May 3, 2022, in which OSHA representatives summarized their recent and planned heat exposure initiatives, including the NEP and ANPRM discussed above and publication of educational materials for employers and employees. During the hearing, stakeholders provided feedback to OSHA about its planned future rulemakings on heat exposure, and one of the most common themes was the need to mandate that employers include acclimatization in their formal heat exposure prevention plans.
We should note that there was significant public interest in the hearing, with over 3,000 registrants for the virtual meeting. Stakeholders widely supported OSHA’s plan to develop a heat exposure standard, sending a strong signal that OSHA will consider and analyze the feedback received, and continue to develop a proposed rulemaking.
Other Plans on OSHA’s Agenda
This is only a sample of OSHA’s regulatory plans for the coming months, with many other initiatives in various stages of progress. These include potential updates to OSHA’s Emergency Response Plan provisions to expand consideration of the range of hazards facing emergency responders and reflect major changes in performance specifications for protective clothing and equipment.
Be sure to read the Spring Regulatory Agenda for the full list of updates, and the links to Reginfo pages for individual initiatives.
Key Takeaways on Regulatory Updates
OSHA is very busy, and their enforcement and regulatory priorities point to far-reaching impacts for businesses across many sectors. It’s a lot to absorb, so let’s slow down for a moment and review major takeaways.
Sharpen your inspections programs
Inspections are one of the common denominators across the standards and regulations we’ve surveyed. For example, the LOTO standard requires periodic inspections to assure that energy control procedures are adequate, the silica rule requires employers to conduct “frequent and regular inspections of job sites” covered by the rules. While we don’t yet know what provisions OSHA will include in an eventual heat exposure rulemaking, it’s likely that employers would need to conduct periodic inspections. All of this means that you’ll need an efficient inspections program to verify compliance with evolving regulatory requirements. The VelocityEHS Safety Solution can help by making it easy to develop tailored, site-specific inspection checklists you and your workforce can easily and rapidly deploy from anywhere.
Incident management
OSHA’s NPRM to update electronic reporting requirements would require many establishments already submitting 300A data to begin electronically reporting data from Forms 300 and 301 as well. Our Safety solution can help there by providing simpler ways of reporting all workplace injuries and illnesses, maintaining documentation in a centralized location, and generating the required OSHA forms. OSHA’s planned inclusion of medical removal provisions in the updated RCS standard provides additional incentive to improve recordkeeping practices, since medical removable cases count as recordable injuries.
SDS/Chemical management
OSHA may issue a final rule to update the HazCom Standard within the calendar year or in early 2023. When they do, they’ll kick off a compliance scramble that will impact businesses throughout the chemical supply chain. Chemical manufacturers of aerosols, flammable gases, and desensitized explosives will need to re-classify many products, re-author SDSs, and produce new shipped container labels reflecting the new classifications and revised label elements such as hazard statements and pictograms. Downstream users of chemicals will need to prepare for an influx of revised SDS documents and labels and train their workers on all updated hazard information. Our Safety Solution makes compliance easy by helping you maintain an up-to-date SDS library that you and your employees can access from anywhere via the cloud, and printing accurate secondary/workplace container labels aligned with the updated SDSs.
Better data for better decision-making
To stay on top of a shifting regulatory landscape, you’ll need to stay agile. That means ready access to key safety data so you can track progress, shift your approach when need, and make more informed decisions to drive continuous improvement. With our Safety Solution, you’ll have access to customizable dashboards and real-time performance reports with automated report sharing features so you and your most important team members will always have access to the information you most need, when you need it.
Be sure to follow us on LinkedIn too, so you can always get the latest updates on the worlds of EHS & ESG.
Let VelocityEHS Help!
It’s easier to stay agile if your tools are agile, too. Our Safety Solution, part of the VelocityEHS Accelerate ® Platform, gives you the support you need to keep up with your most important safety tasks and be better prepared for OSHA’s next enforcement or regulatory actions.
Check out our Safety Solution page to learn more about how we can help you be safer and more sustainable, or to request a demo.