Thinking About Safety Management Software? Think About JSA Software, Too
Posted on March 6, 2024 | in Operational Risk
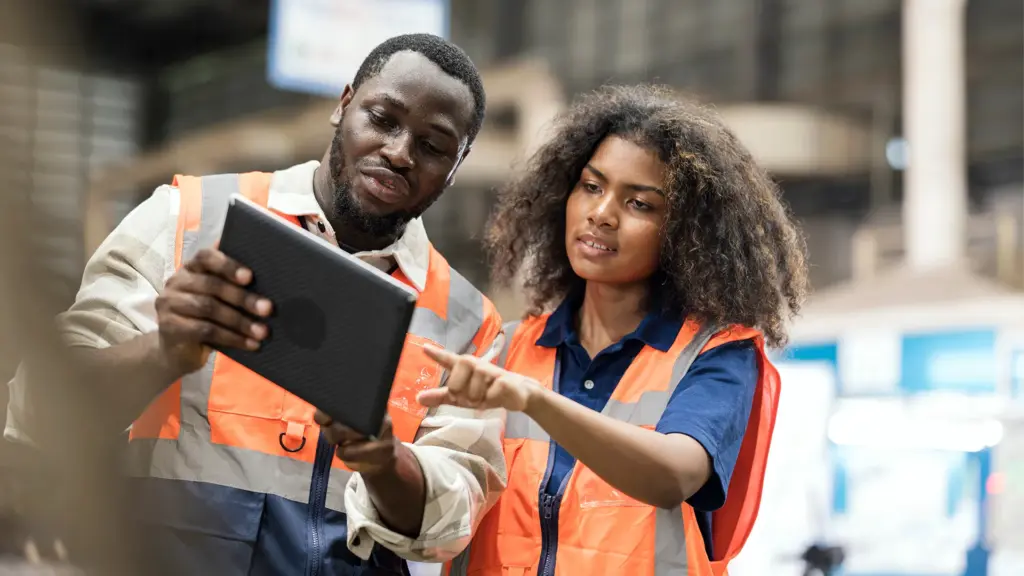
by Phil Molé, MPH
EHS professionals are always seeking out ways to improve their workplace safety management programs, and implementing a safety management software system represents a major milestone along that journey. Good safety software simplifies key tasks such as safety data sheet (SDS) management, completion and tracking of inspections, incident investigations, training, and management of follow-up actions while reducing the time, effort, and resources required to effectively manage workplace safety. Unfortunately, many EHS professionals fail to make the most of their safety software purchase because they overlook the fundamental connection between safety and risk management and how operational risk management techniques like job safety analysis (JSA) can equip them with insights that drive greater levels of safety performance. The EHS professionals who think about JSA software stand to gain significant advantages and benefits.
In what follows, we’ll discuss why organizations looking to implement safety software should also think about JSA software capabilities to capitalize on those insights and get the most from safety software.
Operational Risk Management is the Foundation of Safety Management
Everything EHS managers do really comes down to managing and controlling risk. A brief distinction between two often confused terms, hazards and risks, will help to illustrate this point.
First, remember that “hazards” and “risks,” while often used interchangeably, have very different meanings. “Risk” describes the potential likelihood of something bad happening, coupled with the expected severity of outcome if it happens. A “hazard” is a condition that leads to risks and can be a physical factor you can see (e.g., chemical storage areas, equipment with dangerous exposed parts that can cut or strike an employee), an operational factor like prioritizing production goals at the expense of safety, or a human factor like hazard perception, stress, or fatigue.
These categories of hazards can interact and mutually reinforce each other. For example, operational factors such as long work shifts and a solitary focus on production goals can lead to human factors such as exhaustion and decreased awareness of risks.
The chart below shows some examples of hazards, associated risks, and potential risk outcomes.
Types of Hazards | Safety Risk | Potential Outcomes |
Chemical storage area for toluene | Employee exposure | Headaches, nausea, or loss of consciousness, and potentially hospitalization and days away from work |
Cluttered walkway | Trip/fall | Injury, including potential hospitalization and days away from work. |
Defective backup light on forklift | Collision | Injury of driver or employees in the area due to involvement in a collision, with potential for hospitalization and days away from work. |
As you can see from this discussion and the chart above, the underlying reason for safety incidents such as occupational injuries and illnesses is the presence of hazards that cause risks. The job of an EHS professional is to identify and address these hazards and implement appropriate controls to reduce the likelihood of an incident or injury happening and/or reduce the potential impacts if they happen.
Many Safety Management Tasks Are About Risk Management
When you reflect for a moment, you’ll see that all your safety management activities are, at their foundation, risk identification and control activities. For example:
Inspections
Why do you conduct inspections? Well, you might answer because some inspections are required for compliance with workplace standards and regulations such as inspections for hazardous waste storage locations, inspections of powered industrial trucks (PITs) such as forklifts, or inspections of fire suppression systems and other emergency response equipment. Other inspections may be required by internal management policies, by manufacturers’ specifications, or are just common-sense aspects of safety management, such as ensuring that walkways are unobstructed.
However, there are deeper objectives to inspections beyond simply checking a box. In the US, OSHA requires employers to inspect their PITs precisely because failing to inspect your PITs makes an incident more likely to occur, due to equipment failure such as loss of hydraulic pressure that can result in a falling load and potentially serious injury or death. When you conduct your inspections, you’re really looking to identify hazards so they can be addressed before the worst happens – i.e., to reduce the risk of adverse outcomes.
Incident Investigations and Reporting
This category may have a little less obvious of a foundation in risk management because, by definition, you conduct an incident investigation after an incident such as an occupational injury, a first aid incident or a serious “near miss” or “close call” happens. So, it’s important to reflect on the underlying reason why you’re doing the investigation and filling out the required forms. It’s not just a bookkeeping exercise. You’re trying to gather information about the underlying reasons, or root causes, why the incident happened so that you can address those causes and prevent the incident from recurring. That’s why, for instance, OSHA designed Form 301(“Injury and Illness Report”) to capture very specific details about why and how the incident happened, as the screen capture below shows.
Employers covered by the OSHA Injury & Illness Recordkeeping Standard need to complete Form 301, including the fields shown above, within 7 days of learning that a recordable injury or illness happened. Employers not covered by the Standard should have a process for mapping out the causes of a serious incident, so that the employer can have the information they need to identify and control the associated risks.
Safety Meetings
There are many reasons for having safety meetings, and many different teams or stakeholders who may be involved in them. Meetings build employee engagement (an important aspect of safety management, as you’ll soon learn more about) and give you a chance to share details about safety performance with your people, and to hear from them, in turn. But what’s the endgame? You’re using safety meetings to find out about things that you, as an employer, need to know to manage safety effectively. Specifically, you’re finding out about risks, as employees share details of unsafe conditions in their work areas, so that you can then gather additional information about the issue and then develop and implement appropriate risk controls.
Employee Engagement is Central to Safety and Risk Management
As mentioned above, employee involvement in safety management is an important ingredient for success. Even so, many companies historically have failed to provide their people with direct opportunities to contribute to key safety tasks. This fails to utilize the diversity of their knowledge, experience, and skills, while simultaneously saddling EHS managers and perhaps a small safety team with the bulk of the workload. This situation isn’t fair for anyone involved (or not involved) and greatly increases the likelihood that major workplace risks will go unidentified and uncontrolled.
It’s precisely because of considerations like these that the developers of ISO 45001, the international standard for occupational health & safety (OH&S) management emphasizes the importance of involving all employees in safety management. Section 5.4 of 45001 states:
“The organization shall establish, implement and maintain a process(es) for consultation and participation of workers at all applicable levels and functions, and, where they exist, workers’ representatives, in the development, planning, implementation, performance evaluation and actions for improvement of the OH&S management system.”
Section 5.4 goes on state that the organization needs to emphasize the consultation and participation of non-managerial workers, the group most often excluded from involvement in safety management tasks, and lists some of the specific activities they should participate in, including:
- identifying hazards and assessing risks and opportunities;
- determining actions to eliminate hazards and reduce OH&S risks;
- determining competence requirements, training needs, training and evaluating training;
- determining what needs to be communicated and how this will be done;
- determining control measures and their effective implementation and use; and
- investigating incidents and nonconformities and determining corrective actions.
As you can see from the above list, some of the management areas where the developers of ISO 45001 expect to see frontline employees involved are areas involving risk assessment and control. It turns out that a risk assessment method known as a job safety analysis (JSA) is, by its very nature, a perfect tool for assessing and controlling risks and promoting employee engagement in the process.
JSAs Are an Integral Part of a Robust, Proactive Safety Management System
A JSA, also sometimes referred to as job hazard analysis (JHA), is a way of identifying occupational hazards and appropriate controls to reduce the risk of injuries and illnesses. It involves breaking down work into job tasks and paying close attention to employees as they perform the tasks, use tools, and interact with the work environments. Once hazards are identified, you can then initiate corrective actions to reduce risk.
The effectiveness of JSAs (when done right) is widely recognized among EHS professionals and regulators, alike. This includes US OSHA, who’ve published extensive guidance on their use. In this guidance, OSHA concludes that employers can use JSAs to “eliminate and prevent hazards in their workplaces,” resulting in “fewer worker injuries and illnesses; safer, more effective work methods; reduced workers’ compensation costs; and increased worker productivity.”
To complete JSAs, employers need to follow these steps:
- Involve employees: Determine which employees should be involved in the process of creating the JSAs, based on their job functions and familiarity with the specific tasks.
- Review incident records: Identify which areas and associated jobs have the highest injury rates, and especially the highest rates of severe injuries leading to restricted duty or days away from work. Use this analysis to prioritize which jobs need JSAs.
- Preliminary job review: Work with the employees you selected to discuss the hazards they know to exist and ideas for controls to address the risks. Then use this information to further prioritize jobs to focus on.
- Outline the job tasks: Once you have prioritized your jobs based on risk and have an idea where to start, break the job down into several distinct tasks. The idea is to have enough tasks broken out to be able to accurately identify hazards or risks at each step, but not so many that the job becomes overwhelming. Then, describe the controls currently in place, or the additional controls needed to reduce risks to acceptable levels.
JSAs are only effective when employees participate in the process (as intended), allowing EHS professionals to capture important direct experiences and expertise about the tasks involved, their associated risks, and the controls needed to reduce likelihood of accidents and injuries. The process of completing JSAs with employee involvement will foster even more of the kind of “consultation and participation” that ISO 45001 maintains is important for better safety performance.
Think About JSA Software to Get the Most Out of Your JSAs!
Many EHS professionals already know about JSAs and have completed them at some point. However, completing JSAs and getting the most out of JSAs are two different things. Arguably, most EHS managers aren’t doing as much as they can to use their JSAs to improve workplace safety, because they don’t have the right tools. Luckily, operational risk software can help them overcome the limitations of paper and legacy desktop applications.
Here are some of the reasons that you should think about JSA software, and the ways that the software can improve your insights into workplace hazards and reduce risks for your people.
Think About JSA Software to Improve Accuracy
Theoretically, JSAs offer the potential to improve accuracy of your assessment and control of workplace risks, especially because the exercise of breaking a job down into tasks facilitates better identification of risks associated with different points in the job, and it improves likelihood that you’ll be able to choose and implement effective controls. In practice, a lack of standardization in the JSA process itself leads to variability, particularly in the area of risk scoring and assessment, and decreases the reliability of the results. Adding to these challenges, many EHS professionals completing JSAs lack an extensive background in operational risk management, and so they may have uncertainty regarding selection of controls, or determination of the risk reduction factor associated with a specific control.
Think about JSA software so you can overcome these challenges by offering a standardized methodology for conducting JSAs, so your people do them the same way – and the right way – every time. Even better, the best operational risk software enables you to select appropriate controls for identified risks from a drop-down menu, applies industry-standard risk reduction factors, and then automatically calculates risk reduction based on the selected controls. As a result, you’ll significantly reduce potential for errors from selection of risk controls or calculation of risk reduction. That’s a great reason why you should think about JSA software. You won’t have to be an operational risk management expert anymore to do your JSAs like an expert, because expertise is built into the software.
Think About JSA Software to Encourage Better Participation in Safety Management
Recall that ISO 45001 places a premium on “consultation and participation” of frontline workers. Unfortunately, too often the process of developing JSAs is a classic example of how not to encourage employee engagement with safety management. There are many cases in which a person or two from the company’s EHS department completes the JSA, perhaps with involvement of a consultant, the department supervisor, and/or a high-level facility manager. What’s missing in this common scenario is the direct involvement of the frontline workers who regularly perform the job being analyzed and are the most familiar with its risks, and who likely have valuable insights about the controls that should be applied.
One reason the JSA development process often excludes frontline workers is the methodology used. For instance, JSAs existing only on paper or desktop applications are timebound and more physically inaccessible (a point you’ll revisit soon!), and it just isn’t as easy for multiple employees to share responsibility and contribute. Since the JSA document itself is usually just a form providing no additional guidance, employees often don’t have the support they need to know how to effectively complete the JSA, and awareness of that lack of support can be disincentivizing.
On the other hand, operational risk software democratizes the JSA process by letting employees access and participate in the process from anywhere, using a tablet or their mobile device. It lays out an intuitive stepwise methodology with prompts to guide employees through the process so they understand how to best complete the JSA. Another benefit is that it’s easier to share the completed JSAs and associated activities (e.g., implementation of controls) with employees to show them that their participation has had real results in the form of job safety improvements, which engages workers and makes their future participation more likely. Think about JSA software so you can boost participation in risk identification and control.
Think About JSA Software to Make Your JSAs Accessible
Earlier, when reading about the purpose of JSAs, you learned that JSAs are supposed to provide accurate information about risks and controls associated with different tasks within a specific job to inform safe work practices.
EHS management often fails to capitalize on these intended benefits because their JSAs are inaccessible. Anyone who’s had the chance to review JSA management practices at many facilities has most likely seen this effect. Paper JSAs are stashed in a file cabinet somewhere, gathering dust, and once retrieved, they turn out to be long out-of-date. The same is often true of electronic JSA files sitting dormant in a virtual folder on a computer desktop – not many people access them, or even know how to access them.
The best operational risk software solves these problems by making your JSAs accessible from anywhere on either desktop or mobile devices via the cloud. As a result, you and your people can use the JSAs as guidance for working safely. Not to mention, if any significant changes in your job processes occur that affect either the way you need to perform the job tasks or the effectiveness of your associated risk controls, you can easily revise the JSA and reshare the updated document with your people.
Software Provides Enterprise-Level Insights into Risk Trends
A related challenge with JSAs often being manual and inaccessible is that, quite often, it’s very labor intensive and time consuming to extract actionable information out of them.
With operational risk software, you can easily get the information you need to assess and improve your safety performance. Dashboards will help identify trends in types of hazards across your facilities, so you can get the enterprise-level view of risk patterns you need for better decision making. Think about JSA software. You’ll also be able to verify that risk controls are in place and working as planned.
Let VelocityEHS Help!
Our Operational Risk solution has the capabilities you need to do JSAs right. You get a JSA template configured to your organization’s needs and enterprise-wide visibility of hazards and control activities to help minimize data inconsistencies and monitor the effectiveness of control measures. You’ll also take the guesswork out of control selection for you and your people through access to a control library that has standardized controls and associated risk reduction factors, and automatic calculation of risk reduction based on application of selected controls. Most importantly, you’ll have the insights you need to assess performance and prioritize your workplace improvement efforts.
If you’re looking for just the right safety software, we can help you there, too. Our Safety Solution gives you just the support you’re looking for, with 24/7 access to electronic SDSs from anywhere, easy completion of inspections and incident investigations using a mobile device, seamless initiation, prioritization and tracking of follow-up actions, and much more.
Contact us today to learn more about how we can help you get the most from your JSAs and help you build a safer and more sustainable workplace.