Not everyone who manages workplace risk is a professional risk manager, or needs to be one. If you’re an EHS manager at a facility of any size, you need to get a good handle on identifying and controlling all of your EHS risks. You may have trouble finding the guidance you need, especially given the number of tasks on your safety “to do” list, and especially since many organizations in all industries struggle to move from reactive to proactive management strategies. This new blog series “Introduction to EHS Risks” is for you.
In this first installment, we’ll provide a broad survey of EHS risks, provide a working definition of risks, and review some of the major sources of workplace risks – including some that might not be so obvious at first. We’ll also review a real-life example that shows that major accidents that impact our business and our reputation can happen in facilities of many sizes and risk levels, across many different industries.
We’ll cover even more examples of risk scenarios in different industry settings in later installments, and also talk about how to prioritize risk, how to manage risk through better collaboration across all areas of your business, and how use of tools called risk bowties can help improve all areas of risk management. In fact, we’ll discuss how risk management itself can help foster better engagement with safety and stronger EHS cultures.
With those introductions out of the way, let’s get started!
Challenges of EHS Management
Let’s begin by reviewing the challenges of EHS management. Not all of the description below may apply to you, but I’m betting some of it does.
Maybe you have some academic training in EHS, but had previously held positions not directly involved with workplace safety, such as in consulting, or work in analytical laboratories. If so, you’re finding that corporate EHS management is a whole different challenge, because it has so many moving parts, many of which involve relationships between departments and people. Figuring out the strategy for navigating all of the different needs and expectations of different parties in your organization can sometimes feel like solving a giant puzzle, and you may not even be sure you have all of the pieces.
Perhaps instead, you’re someone from a field outside of EHS, such as Human Resources, Quality, or Facilities Maintenance, and have decided (or have been “voluntold”) to pivot your role to include safety management responsibilities. In your previous roles you may have had some people and relationship management skills, but you don’t yet have the background knowledge and familiarity with the full scope of your job to successfully apply that knowledge.
However you came to your position in EHS management, you probably find that you have a long punch-list of tasks that never seems to get any shorter. It takes so long to just enter your key data from inspections and safety meetings and other EHS activities, and to track and follow up on actions, that you don’t have time to move from just a default level of business toward a more proactive approach. You’re too busy responding and documenting yesterday’s incidents to actively strategize about preventing tomorrow’s incidents. And you might often find yourself surprised when a workplace accident occurs, because they might reveal sources of workplace risks you hadn’t previously considered.
In short, you sometimes feel overwhelmed by the sheer number of things to do, and don’t even know where to start.
The good news is that better risk management can help. Having a better understanding of all of your sources of risk before incidents happen, as well as the knowledge about to how prioritize risks to better plan and manage workplace risk controls, can help you pivot toward a more proactive approach. As you move ahead with your improved risk management strategies, you’ll also find yourself better navigating the landscape of company relationships necessary to do your job effectively and efficiently. The pieces of the project and people management puzzle will start to fall into place.
While we’ll revisit this theme throughout this series, we’ll lay out the basic premise right now: Since everything you do as an EHS professional involves identifying and controlling risks, development of your risk management skills is central to your job effectiveness. It’s also central to developing and sustaining a robust EHS culture where all employees have important roles to play.
Risk management is the glue that holds your safety management system together.
Hazards, Risks, and Opportunities
A good place to start our review of EHS risks is with the definitions of “hazards,” “risks,” and “opportunities.” Even many EHS professionals you’ll encounter often use the terms “hazard” and “risk” interchangeably, and they’re not the same thing.
I like using the definitions of these terms from ISO 45001, the international standard for occupational health & safety (OH & S) management systems. You’ll find ISO 45001’s definitions in the image below.
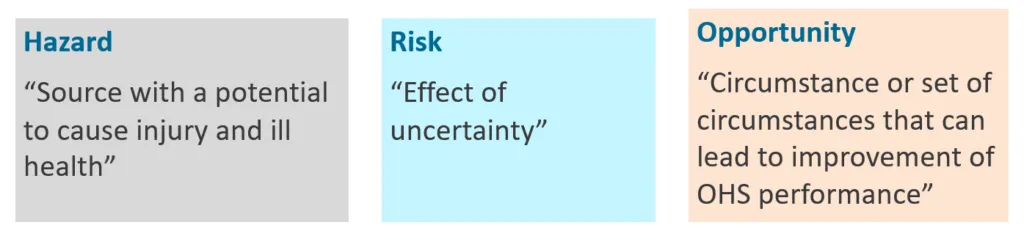
I realize that the definition of risk as an “effect of uncertainty” may seem baffling in its simplicity – kind of like a Zen riddle. But it does introduce a key concept of “uncertainty,” which is getting across the idea that risk is really a matter of statistical probability. A note associated with the definition expands on this by noting that “risk is often expressed as a combination of the consequences of an event and its associated likelihood.”
One of the takeaways is that hazards are conditions that give rise to risks. For example, a wet floor in a walkway is an unsafe condition, aka a hazard, that leads to risks of accidents such as slips and falls, or possibly electrocution. Hazards don’t always need to be physical things we can see and directly measure, as we’ll soon see – they can also be conditions such as fatigue that result from the way we’ve structured work tasks, schedules, and productivity expectations.
Sources of EHS Risks
OK, so now we know what risks are, and the difference between hazards and risks. Let’s move on to talk about some of the sources of workplace risks you may have. Major sources of risk are shown in the diagram below.
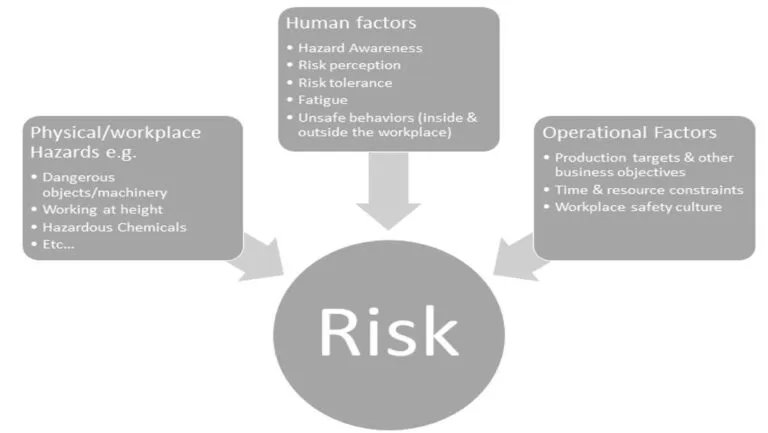
Note that the categories above can interact, too. For instance, the operational factor of production targets can lead to the human factor of fatigue, and both can lead to increases in risk – in the potential for occupational injuries and illnesses. This example also demonstrates the point that there’s not always, or even often, a simply 1:1 relationship between hazards and risks, where each hazard leads to one and only one risk. Hazards can combine their influence to increase the probability of certain risks. A common situation involves work-related anxiety, or psychosocial risks, which reduce employee hazard awareness and combine with physical workplace hazards to create greater likelihood of an occupational injury.
The chart above should hopefully provide a good illustration of the earlier point that everything we do as EHS professionals involves risk management. Many EHS professionals, even those who’ve been in their roles for a while, still often focus only the hazards they can “see” – the physical hazards on the left side of the diagram above. In doing so, they ignore the two huge hazard categories of human factors and operational factors, and also ignore the way those two sources of hazards interact.
Your success in your role as an EHS professional depends on your ability to take an integrated view of risk, and facilitate the plans needed to identify and address them. That means you’ll need to look beyond the obvious sources, like hazardous chemicals and dangerous equipment, and carefully assess all aspects of work. This could include policies, workplace priorities (e.g. “getting things done” vs. “working safely”) and elements of safety culture, such as top management’s involvement in safety initiatives, and whether our employees believe and trust in our safety programs.
As you review the above diagram, think about who you’d need to collaborate with to address those sources of risk. To review and potentially revise employee policies, you’d need the involvement of Human Resources, and to better understand job demands and expectations, you’d need productive conversations with both frontline workers as well as facility and company management.
Effective risk management depends on relationship building, but it can also be a powerful framework for building the relationships themselves.
Categories of Risk
Now that we’ve surveyed the sources of occupational risks to be aware of, let’s take a look at the types of risks you need to consider. The chart below shows six main categories, and examples of each.
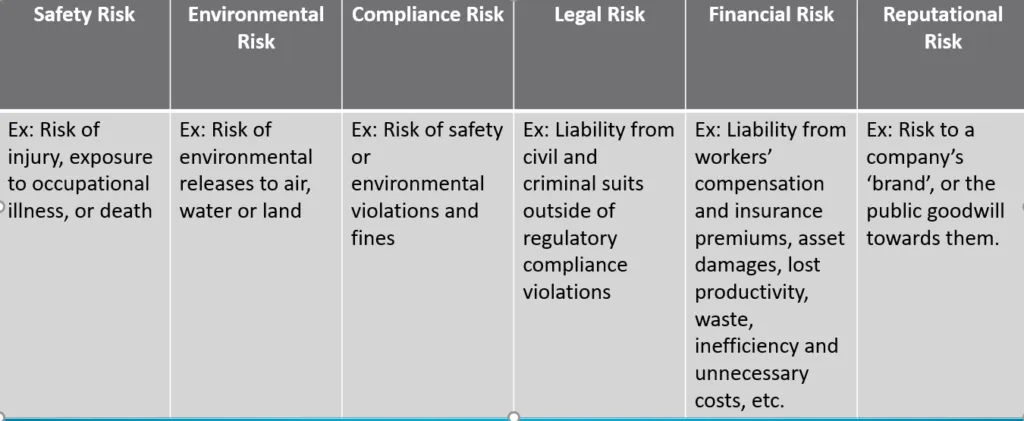
There are some events that might wind up checking the boxes for all of these categories. We might be inclined to think of examples of catastrophic releases at bulk chemical manufacturing facilities for example, and conclude that such a category-spanning event can’t happen to us. And yet, it can.
Here’s a real-life example.
In my past life as a regulatory consultant, I got to meet many different EHS and safety coordinators at many different kinds of facilities. During one visit, at a small manufacturing facility in northwestern Illinois, my site contact told me about an incident that had recently occurred at the end of a shift, after an employee disposed of the remaining chemicals in his containers in into a 55-gallon drum of waste. In doing so, he unknowingly mixed incompatible chemicals and catalyzed a reaction. Later investigations identified that the employee had never received training required for employees who handle hazardous wastes by EPA Resource Conservation and Recovery Act (RCRA) regulations. Additionally, the chemicals in the waste drum were not being stored in the temperature range indicated for safe storage in Section 7 of the SDS.
According to the site representative, an employee in a later shift noticed that the 55-gallon waste drum was bulging outward at the centers so significantly that there seemed to be real potential that the drum could explode. As it turns out, the reaction going on inside the drum was an autocatalyzing exothermic reaction – meaning that as it progressed, it was producing heat and fumes that exerted pressure on the walls of the drum, severely stressing its integrity.
The site’s management evacuated the facility and contacted the local fire department. Luckily, the quick availability of information about the chemicals involved helped first responders determine how to handle the situation. They used fire truck hoses to continually spray cold water against the side of the drum, which allowed the reaction to finish up at a controlled pace, and not happen so fast that the drum exploded. When it was all over, the material left inside the drum looked like 55 gallons of melted basketballs, with no remaining liquid. They’d made it to the other side of a scary situation with no injuries and no property damage.
But, they didn’t make it there without attracting quite a bit of attention. Due the seriousness of the situation, other area fire departments and even county-level officials had mobilized to the site. And as they did so, local media began covering the unfolding events at the facility. Luckily for everyone involved, their story had a happy ending, but if just a few things had gone differently, the consequences could have been horrific.
Here’s how this one incident, that could’ve happened pretty much anywhere, checks all the boxes for the risk categories in the table above:
Safety: If the drum had exploded, it could have severely injured or even killed employees in the vicinity. Toxic fumes released from the drum could also have posed occupational exposure risks.
Environment: Chemical wastes released from the drum could potentially have entered storm water drains and impacted area creeks that received the facility’s storm water discharges.
Compliance: The incident exposed the fact that the company had gaps in the hazardous waste training it provided to its employees. That fact alone exposed them to potential findings of regulatory noncompliance, and notices of violation (NOVs) would’ve been very likely in the event that an explosion occurred and triggered additional Illinois EPA oversight.
Legal: In the event that the drum had exploded and injured employees or members of the community, the company could have found itself facing lawsuits.
Financial: NOVs would quite possibly be accompanies by monetary fines, and lawsuits could potentially result in the company paying compensation to injured parties.
Reputational: Think about the media coverage that occurred at this small manufacturing facility in a small Illinois town, and now think about how much more would have occurred if there had been an explosion, or a serious injury. Think about the times you’ve heard about a major accident at a facility, and how it affected your perception of the company. A company of any size in any industry can have an accident that adversely impacts their “brand” and public perception.
Key Takeaways on Risk
Let’s distill some of the main points so far:
- Hazards and risks are not the same thing. Hazards are conditions that lead to risks.
- Risk is a combination of the likelihood of something bad happening and the severity of outcome if it happens.
- Successful EHS management depends on taking an integrated approach to identifying and controlling all sources of risks (including human and operational factors) and building the right relationships within your organization.
- The main categories of risk are safety, environment, compliance, legal, financial and reputational.
- You don’t need to have a large or complex facility to have a potential for incidents that check all of the boxes of risk categories.
Watch this space for future installments of this series, in which we’ll talk about how to prioritize your risks, considerations for choosing and managing risk controls, and the benefits of using a tool called risk bowties. And finally, by the end of this series, we hope to convince you that risk management is the glue holding your entire EHS culture together.
Let VelocityEHS Help!
VelocityEHS understands the challenges of risk management for EHS professionals in every industry. That’s why we offer Risk Management software that helps organizations of all sizes in all industries manage their risks. We can simplify the process of identifying all risks from all sources, managing risk controls, and engaging your entire workforce in risk management, so you can build and sustain the relationships needed for success.
Ready to see more? Visit our Risk Management page to request a demo with one of our customer solutions consultants today!